With the gauge programming starting to fall in place, I pivoted toward the physical installation. I decided to go with an a-pillar gauge pod, and got to measuring and designing. I whipped up an initial revision with a single gauge pod on it for test fitting. I want to make sure the screen sits in there nicely, nothing vibrates, and I have room for my cables. This test fit will let me figure out exactly how much room I need for everything, if my profile, fitment, and angles are good, so the final version can be sleeker.
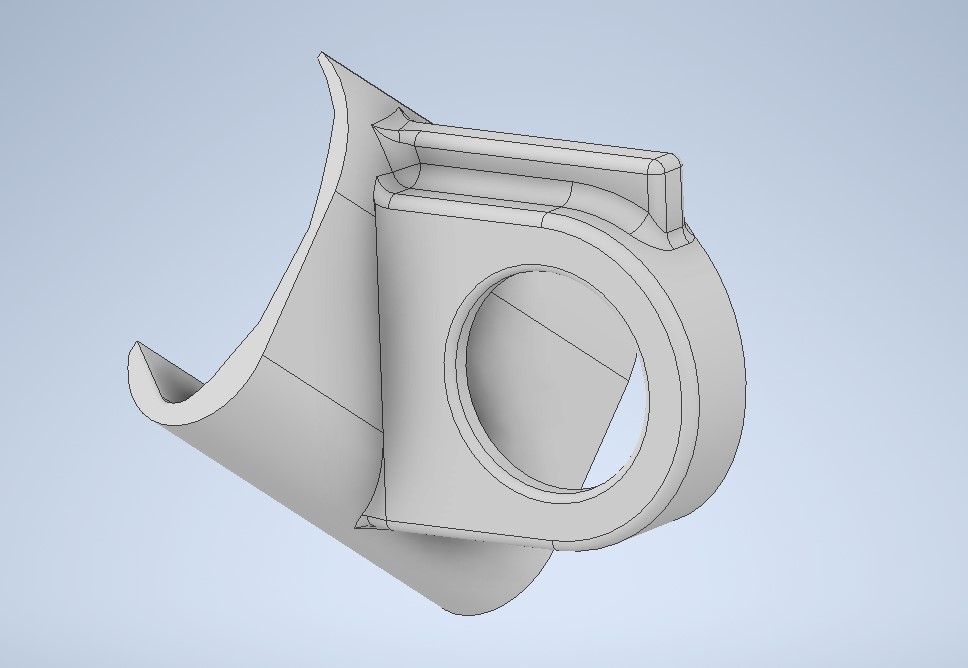
I went to print this out, only to have my printer jam up and create a giant ball of ABS that borked the extruder.
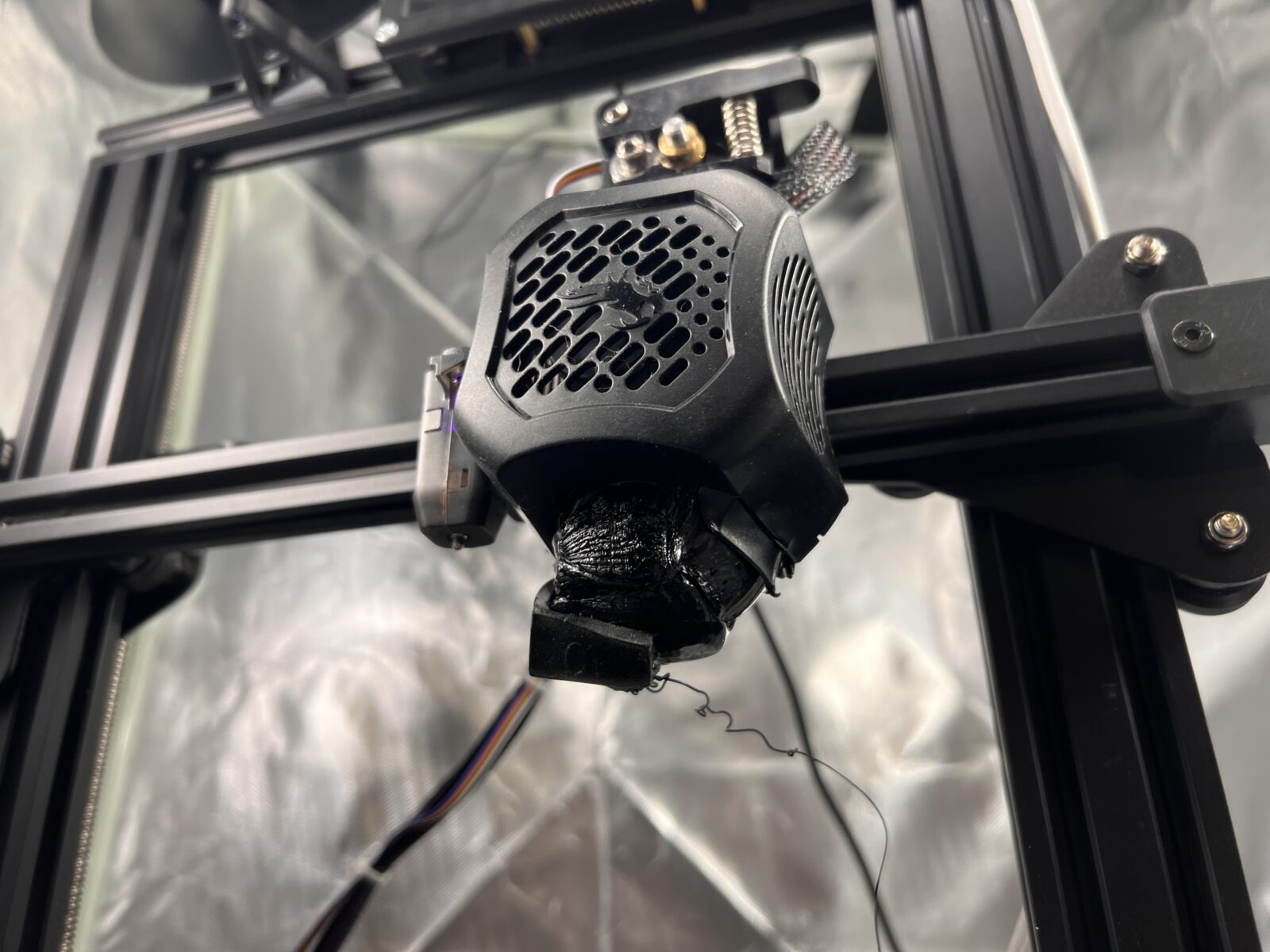

I took that as a sign to go ahead and upgrade to a better direct drive extruder, and why not go ahead and redo the entire control system. With that running and like, 80% good, I went for another print. This thing is difficult to orient because no matter what there's a ton of overhang. On this run, I went ahead and printed upright, but forgot to add supports to the overhang. Unbelievably, the thing actually almost worked

. The gauge pod cantilevered out into space and it printed a bunch of it. Unfortunately, with no support, the ABS actually curved upward as it cooled, eventually going high enough that the extruder caught it on the way past and pulled the part off the bed. Fortunately, it was enough that I could verify the profile around the a-pillar and kind of gauge if the angle looked good.
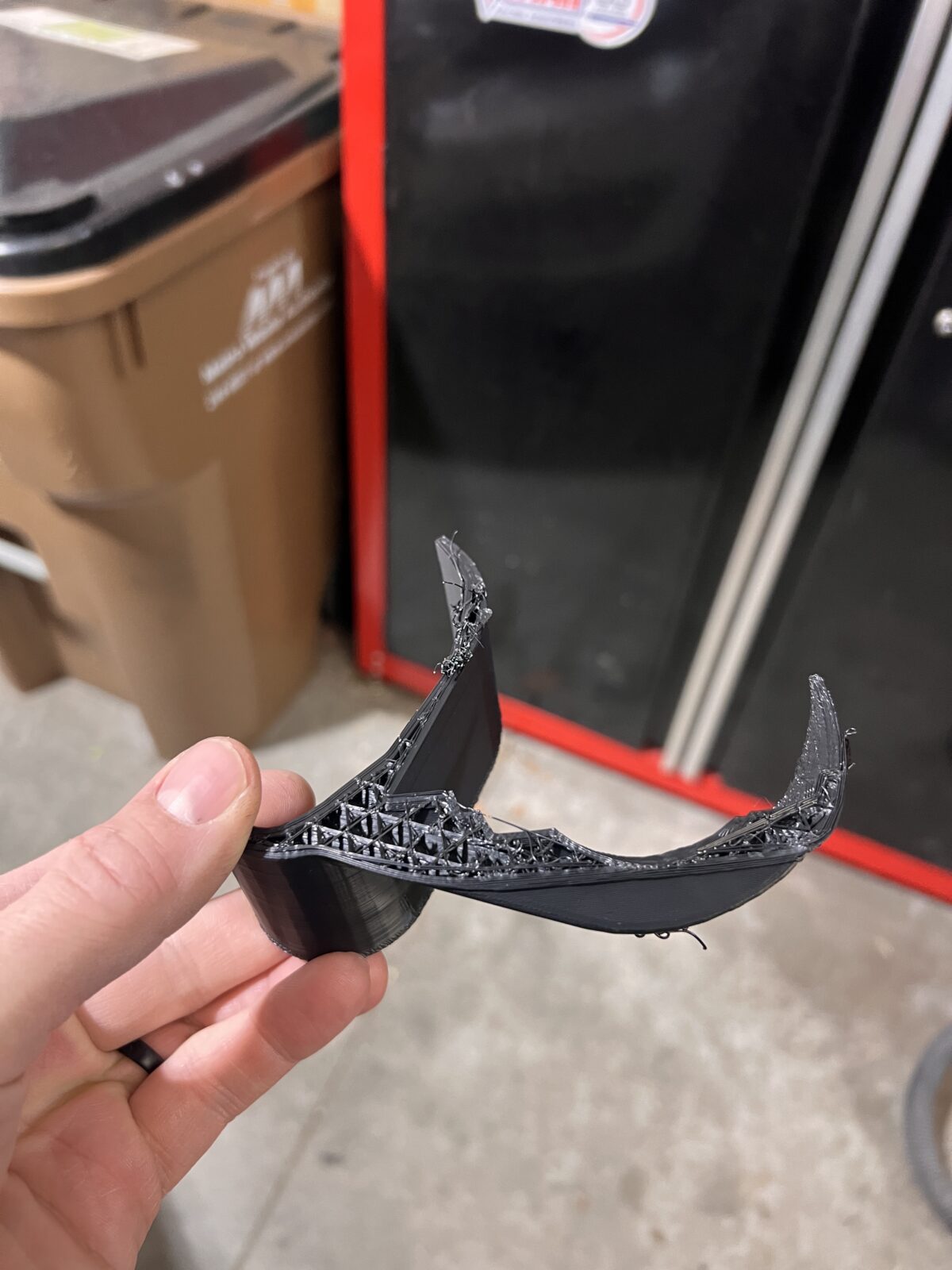
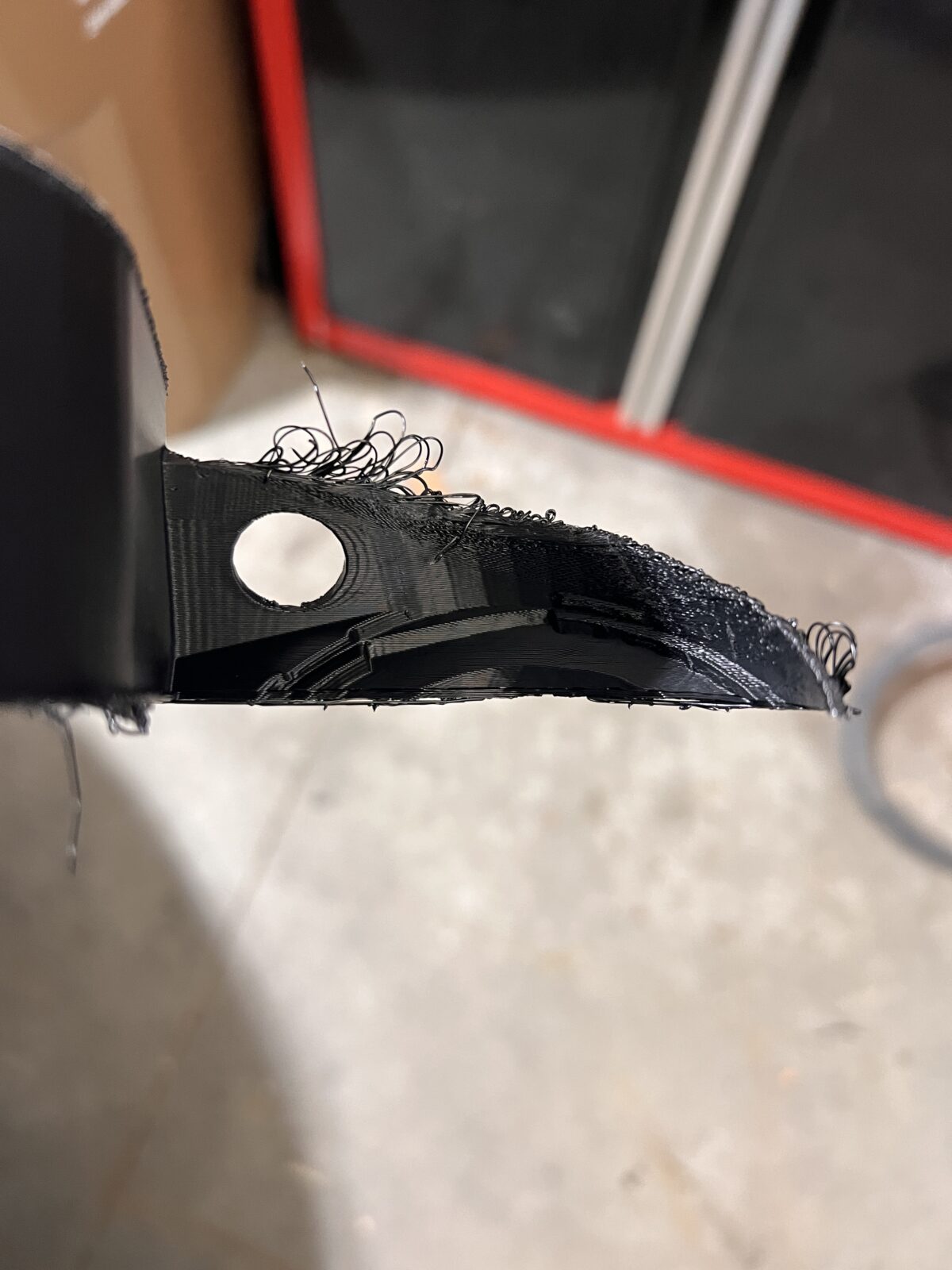
I'm happy with the fitment around the a-pillar trim.
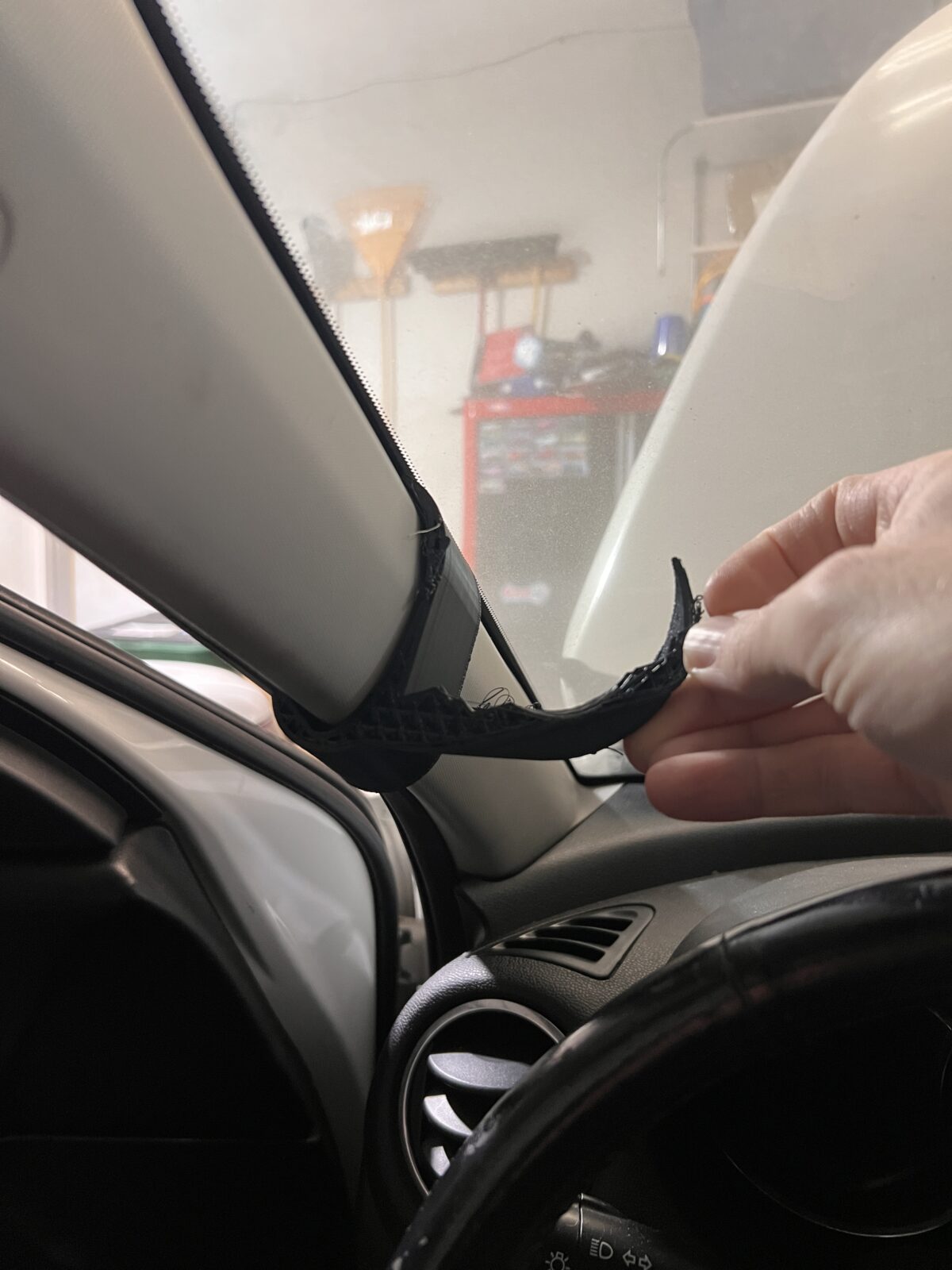
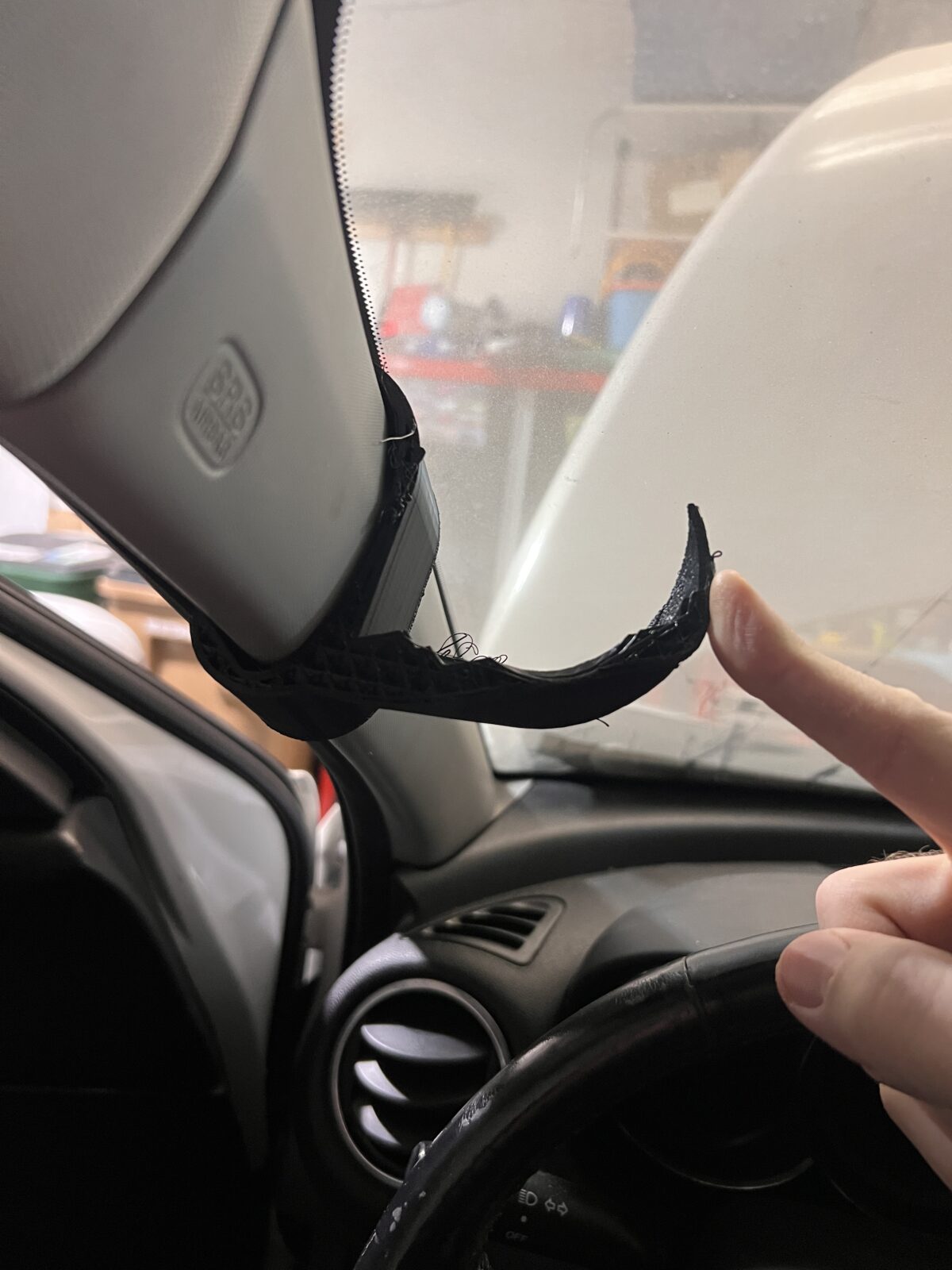
The angle toward the driver looks good. I'll do another print (with support this time) so I can confirm size and fitment and then finalize the design.
As work winds down this week, hopefully I can get back out to the garage and keep pushing forward with finishing the engine bay, electrical, and fuel system. I want to drive this thing in 2025!