Finally got off my butt and took some measurements. Made my own hacky angle plates:
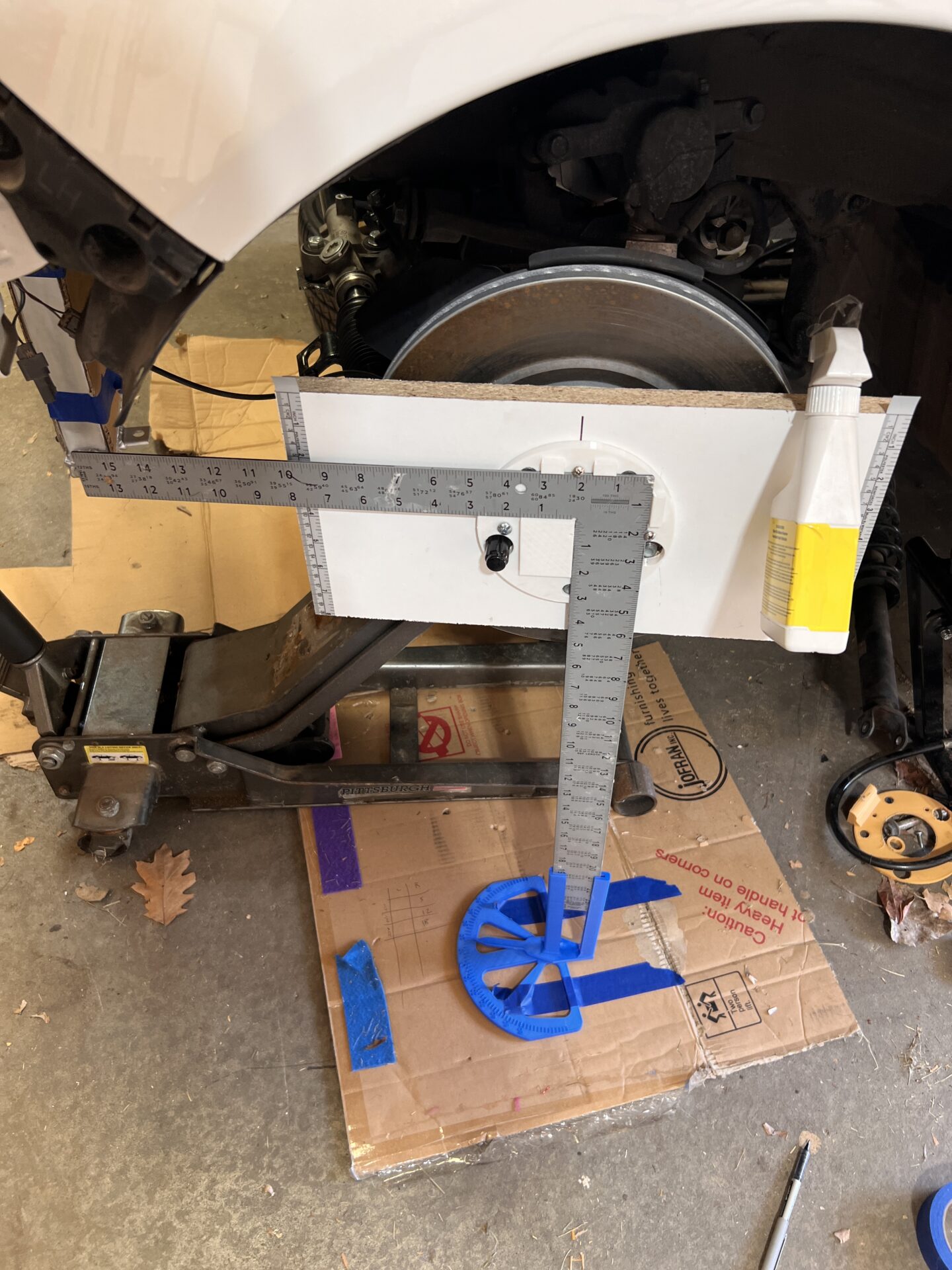
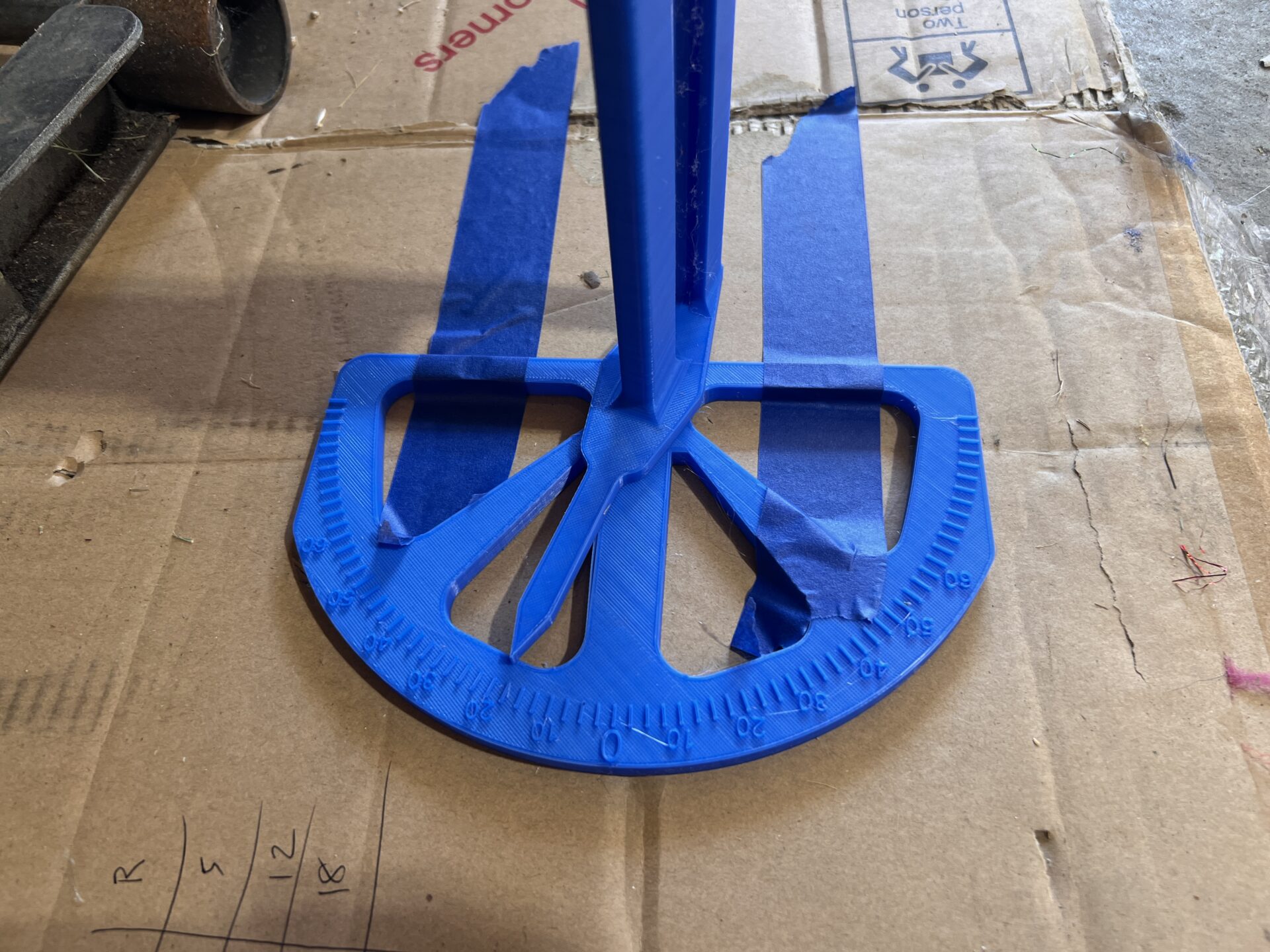
The adapter on the wheel captures the ruler, which extends straight to the ground. I used a jack to put the spindle at ride height. It's not a perfect system but I figured it would at least give me a ballpark answer.
My goal was to see the effects of shifting the rack forward on my Ackermann angle and to decide if I need the little brackets that push the arms back. I found an equation on the
Formula SAE forums to define the steering angle as a percentage of perfect Ackermann.
I set the wheel straight ahead and put the angle readout at 0 degrees. Then I turned the wheel in 1/4 turn increments and recorded the angles. The driver's side had no adapter and the passenger side did have an adapter, so I was able to get measurements with and without my change.
The ruler extended straight down from the centerline of the wheel mounting surface, but due to the scrub radius of the suspension geometry, the ruler didn't just rotate perfectly still, it moved in an arc. I did my best to keep the measurements consistent, but I know there's some error. Here's what I ended up with:
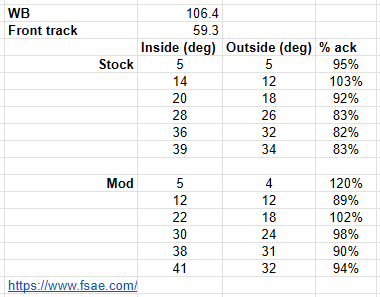
Stock is the rack without my compensation bracket, results are maybe mid-80s, average of 90%. Mod is the rack with my bracket, results are more in the mid-90s, average of 99%.
Is geometry better with the bracket? Signs point to yes. Downsides of the bracket are having homemade components in the steering linkage (danger), stock tie rod boots won't fit (corrosion on a street car), brackets shorten effective tie rod length (bump steer geometry). At this point I'm going to move forward without the brackets, assuming 80-90% of perfect Ackermann will be acceptable and is a good tradeoff for the safety and longevity keeping the stock tie rod retention system in place.