Finished up my DI plugs. I got the actual tools in from Injector Rehab. I like their little taper piece better - obviously the smoother the surface and the thinner the wall the better, so it was nice for expanding the seals onto the plugs. Instead of having a separate pusher and compressor like the OEM tools, they kind of have it combined. My 3D-printed pusher worked better so I used that, and then I ended up going back and forth with my compressor and theirs to get everything seated.
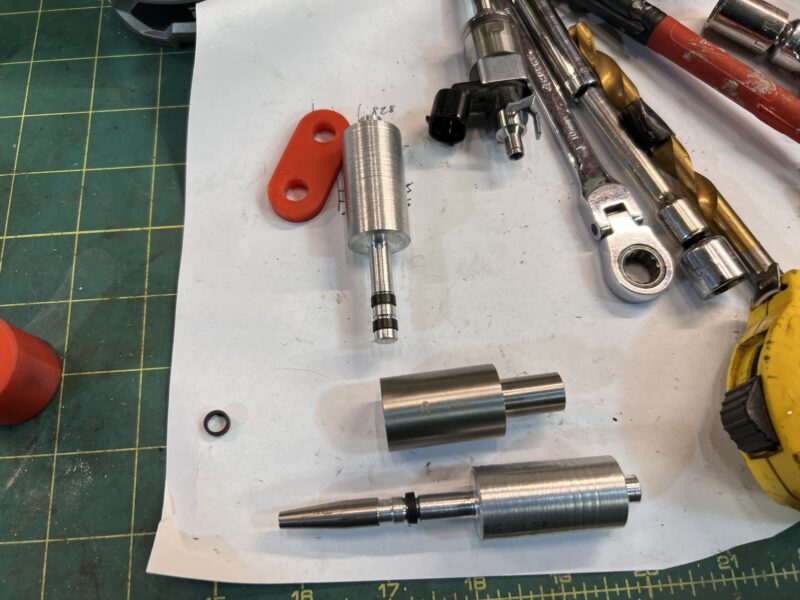
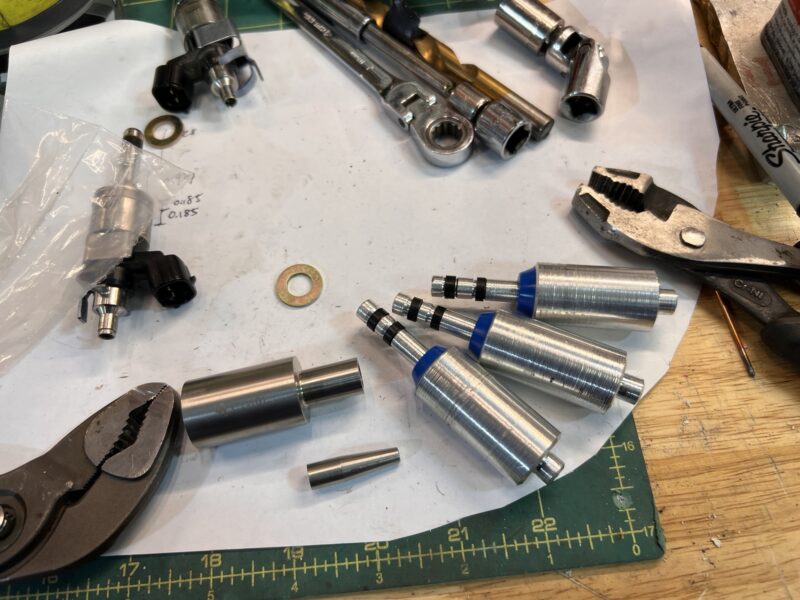
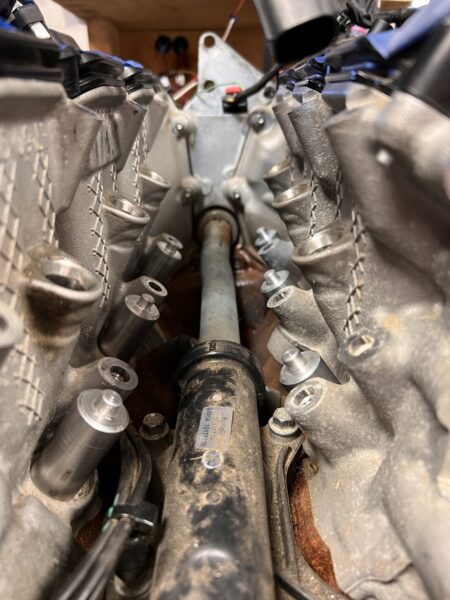
I started poking through my cooling system hoses because I think I want to set it up on the stand and actually get the engine up to temp.
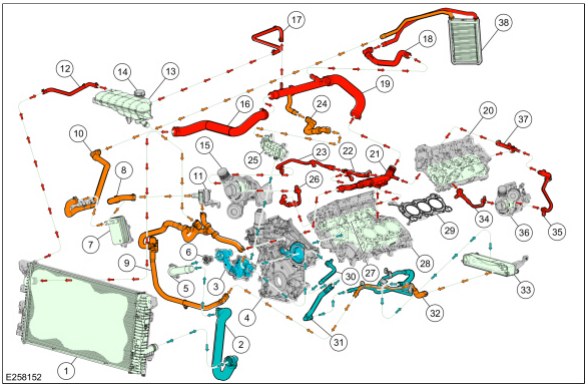
There's a lot there - I'm deleting the EGR so I can eliminate that. The truck it came from had auto start/stop so it had an aux pump to keep coolant moving into the cab for heat even when the engine was stopped, that can go away. It has a loop for the trans cooler, that disappears as well. I ordered an OEM coolant expansion tank, though I don't think I can mount it up front where the F-150 and Mustang have it, as the hoodline is low enough that it wouldn't be the highest point in the engine. Speaking of which, the 2.7 has hot coolant coming out the back of the engine and traveling through an external hard pipe over the top of the intake, then into the radiator (#19). A decent portion of that pipe is above the hoodline, so I might need to do some reconfiguration. The other thing I found (or didn't find, actually) is the flex hose on the back of tube #19 that connects it to #21. I spent a good bit of time digging through all of my shelves and boxes and can't find it. I know I had it out when I was fitting the engine as the firewall requires a touch of clearance to get it to fit, so a bit of time wasted there.
Next I wanted to confirm clutch fitment. When I first got this engine I was pleased to find that the crank had already been factory machined for a standard Mustang pilot bearing.

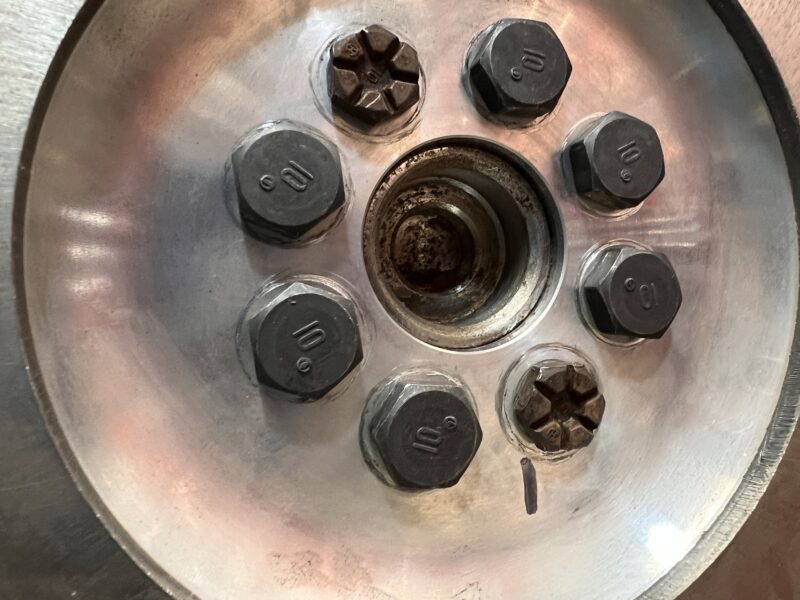
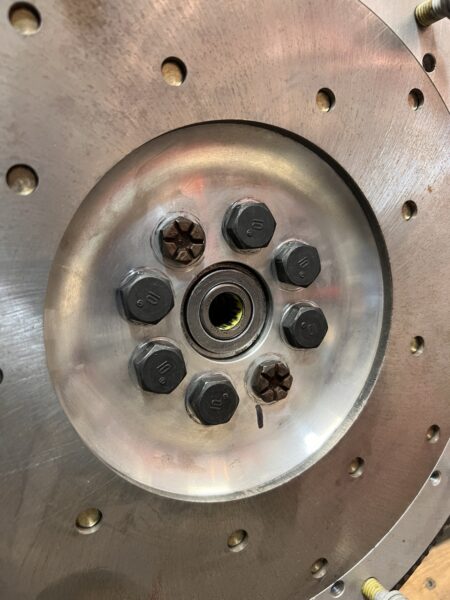
I wanted to measure pilot bearing depth. The V6 Mustang came with a big thick dual mass flywheel (33lbs!):

I decided to forego that and just got a Coyote clutch kit. The difference is that the slave cylinder in the transmission is expecting some extra thickness, so a spacer is needed behind it when running the thinner Coyote setup.
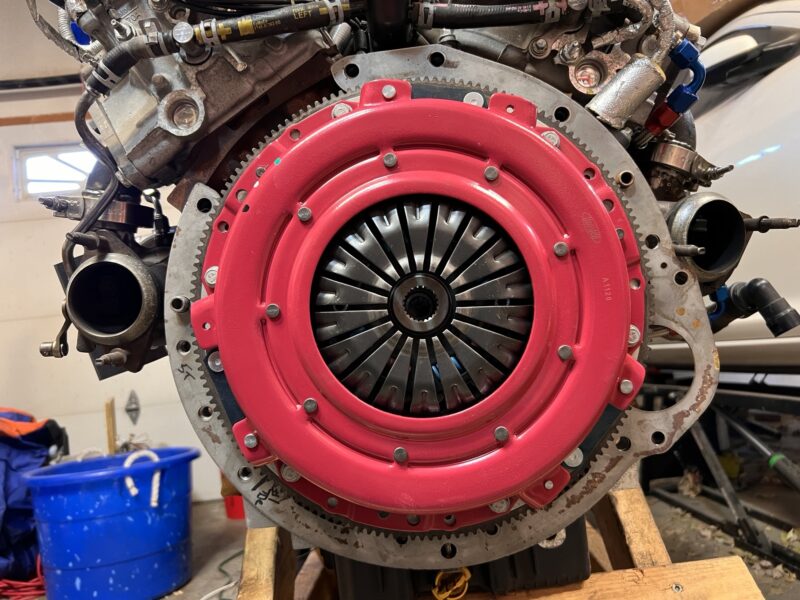
I, once again, wasted a whole lot of time going through all of my boxes and shelves trying to find my clutch alignment tool. Couldn't find it anywhere, so I just eyeballed it. I may have to 3D print a replacement rather than waste a bunch more time looking through all of my junk. I don't know why I couldn't just leave the alignment tool in the box with the clutch

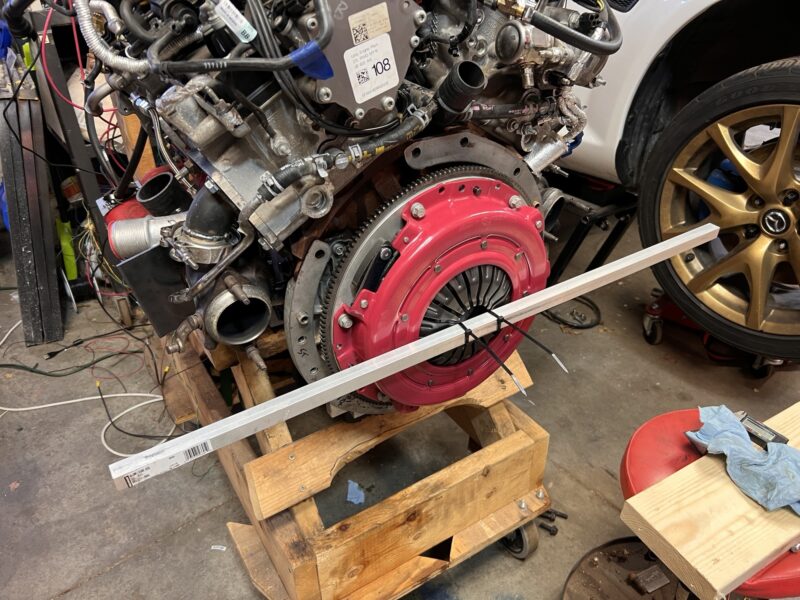
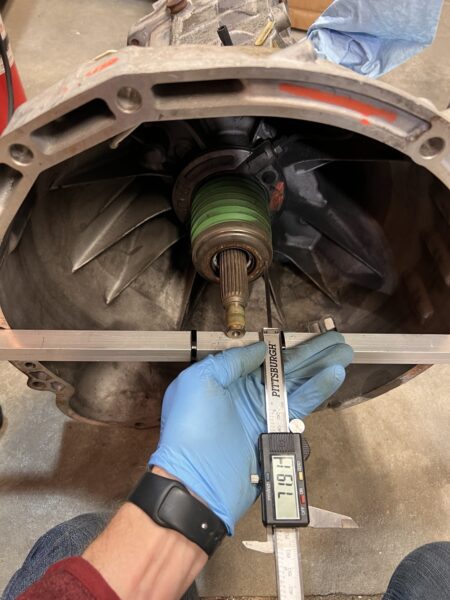
The clutch slave is at 72mm fully extended and 108mm fully compressed for 36mm of total stroke. The clutch fingers are 85mm proud of the mating surface with the clutch plate installed. So in this state I would only get 13mm of preload and I'd probably pop the slave apart if I pressed the clutch pedal.
I want about a 5mm buffer to account for clutch wear, so I want the clutch to preload the slave down to 103mm. 36-5-13 = 18mm - the math tells me I need about 18mm more preload. That lines up with the
kits available, which are 3/4" (19mm).
I have some 1/4" stainless steel plate on the way, I'll use that to make hold-down brackets for the DI plugs. My replacement fuel pump is here, but I'm still waiting on the sock. Not interested in smoking another fuel pump.