More progress. Finished up the ECU connector and heat-shrinked all of the pins I used. I need to figure out what to do with the remaining pins - some may have voltage on them and some may be grounded and I wouldn't want those touching each other, so I'll have to think about that.
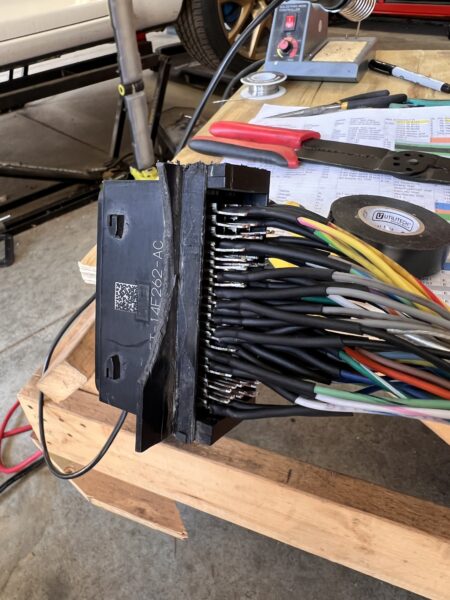
Pins I'm not using:
Fuel pump + 86 Ye/Vt
Fuel pump - 107 Gn/Vt
Evap purge 46 Wh/Bn
Turbo bypass 80 Bn/Wh
HP fuel pres 71 Bn/Bu
LP fuel temp 31 Gn
Turbo boost p 94 Ye/Bu
CAC temp 10 Bn/Wh
EGR pres 49 Wh/Vt
EGR v - 19 Bn/Ye
EGR v + 40 Bu/Gn
DPF 32 Gn/Og
Exhaust Pres 97 Gy/Bu
CHT2 8 Bu/Gy
EGR temp 96 Gy/Vt
Sigret 99 Gn/Bu
Inj1 2 Gn/Bu
23 Ye/Bu
Inj2 66 Gy/Ye
45 Bu/Og
Inj3 44 Vt/Gy
65 Gn/Vt
Inj4 1 Ye/Og
22 Bu
Inj5 43 Bn
64 Wh/Gn
Inj6 41 Gn/Wh
20 Bn/Vt
From there I got the harness divided between stuff going into the engine bay and stuff staying inside the car, then separated into the engine bay harness into the ECU plug and other engine bay stuff - flex fuel sensor, cooling fan control, A/C control, alternator control, etc.
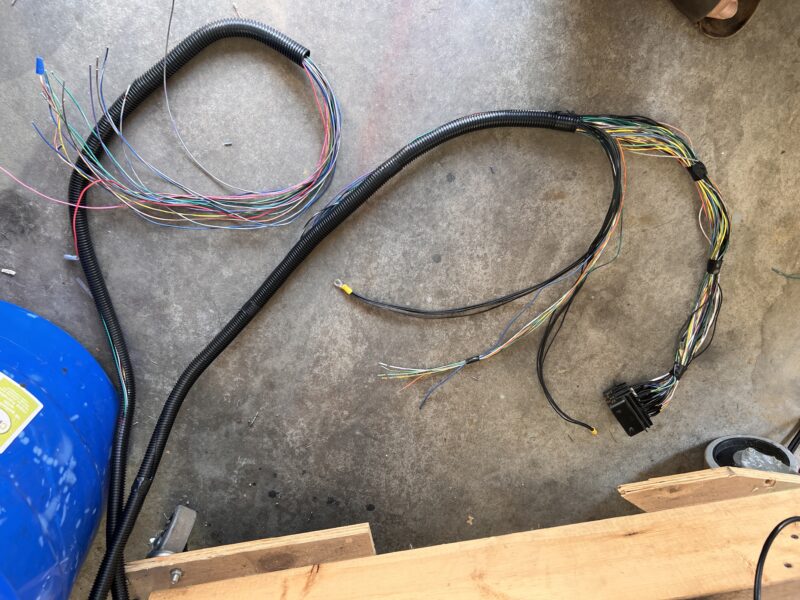
Time to test my plug.
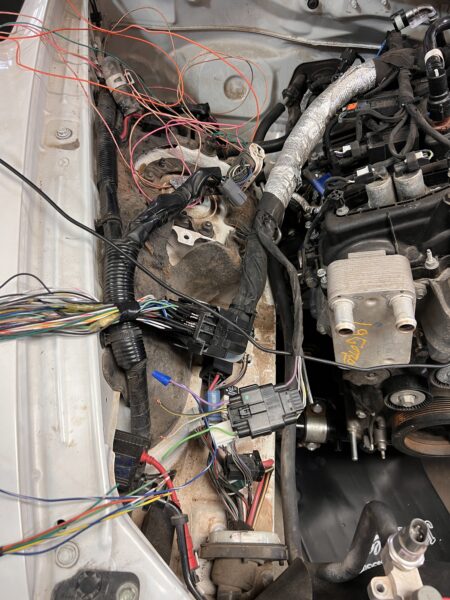
I confirmed spark on all 6 coils, but couldn't tell if the injectors were firing. I couldn't hear anything clicking but the injectors are buried under the intake manifold so I couldn't get to them. I also saw readings coming from the sensors for fuel pressure, oil pressure, crankcase pressure, wastegate control pressure, MAP, IAT, and coolant temp.
Then I hooked up the external DBW box to the RX-8 pedal and the Megasquirt CANbus and confirmed that all worked like it's supposed to.
Since my engine originally came with a new version of DBW throttle that combines a single analog feedback with a digital/serial feedback, I had to swap to the earlier model TB with dual analog feedbacks in place. I took out the sixth wire from the throttle and routed that back through one of the now-unused pins from the external coolant pump pigtail to get my signal back to the DBW box.
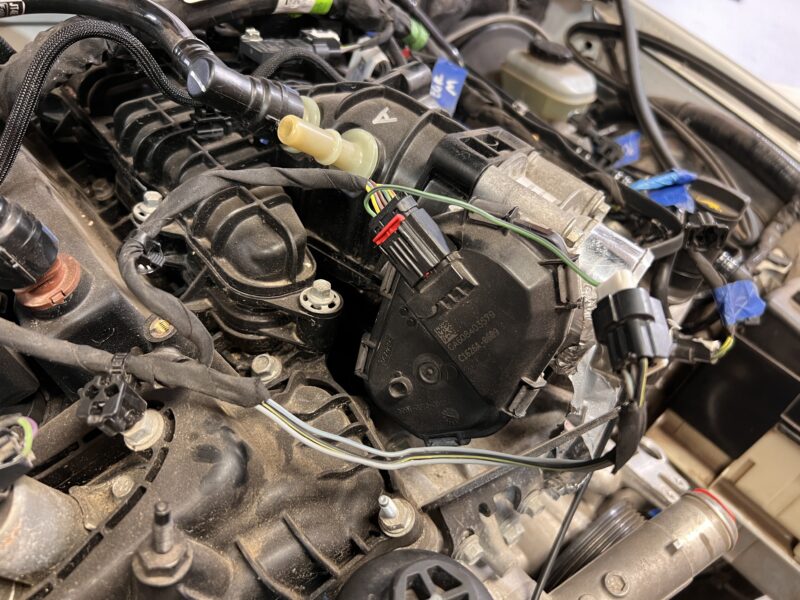
After all of THAT I hooked up the two CANbus wideband O2 controllers (14point7 Spartan3) and made sure they were configured and talking. Upgrading their firmware required running a shady app in the command line and my MacBook Air with virtualized Windows couldn't do that - it kept complaining about missing DLLs. So I grabbed my son's cheap Win11 laptop and got the firmware updated, then used the MacBook to send the required serial commands to change the CAN ID on one of the boxes so I can run them both simultaneously.
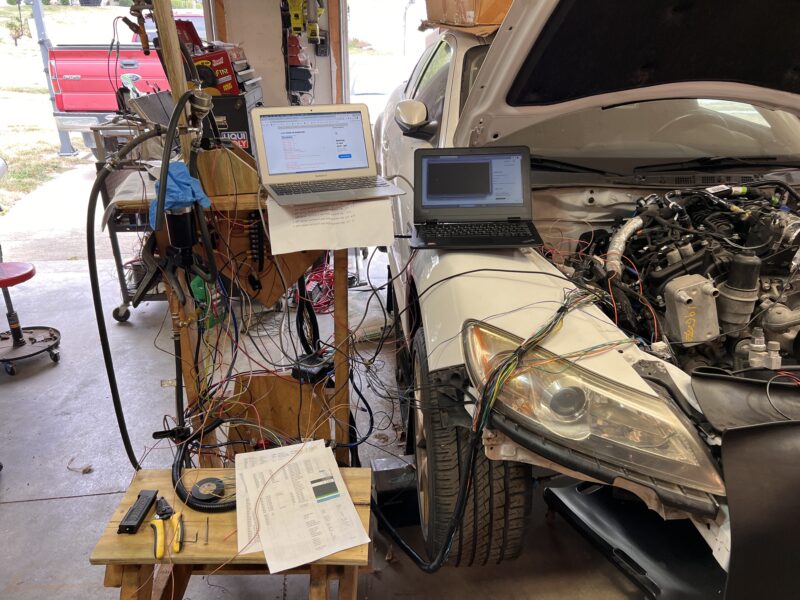
Weirdly, all of that was fun. I needed to confirm injector operation, so I went ahead and pulled the upper intake.
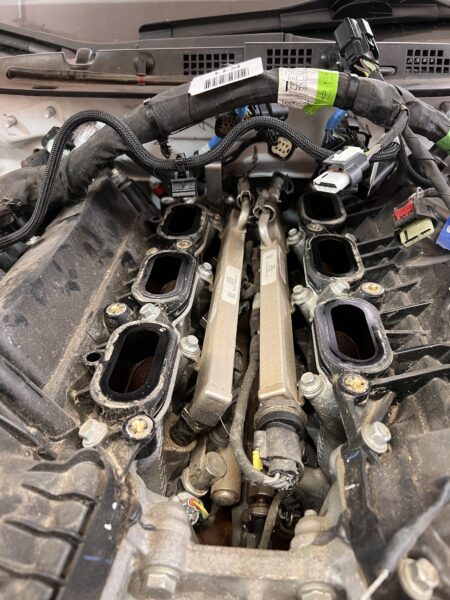
Port injection rails up top, direct below. At this point I realized I wired up to the wrong fuel pressure sensor. The drawings showed one combination pressure/temperature sensor, and one standalone pressure sensor. I had guessed that the combo sensor would be in the direct rail but I guessed wrong, so I'm going to have to swap my pressure reading over a pin. I'm already getting fuel temperature from the flex sensor so I won't waste another ECU input on redundant info. Fuel temperature at the rail is most crucial for starting a direct injected engine, so that doesn't really do anything for me.
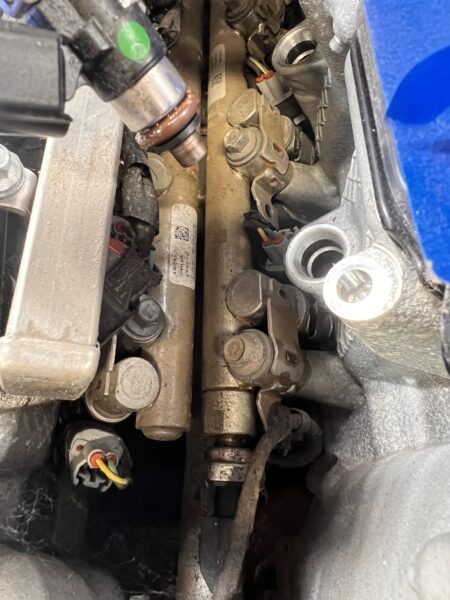
Upper injectors are 29lb/hr I believe. Good enough to supplement the DI system, but not enough to support good horsepower on their own. I'll confirm they work for startup, then swap them out for some bigger boys.
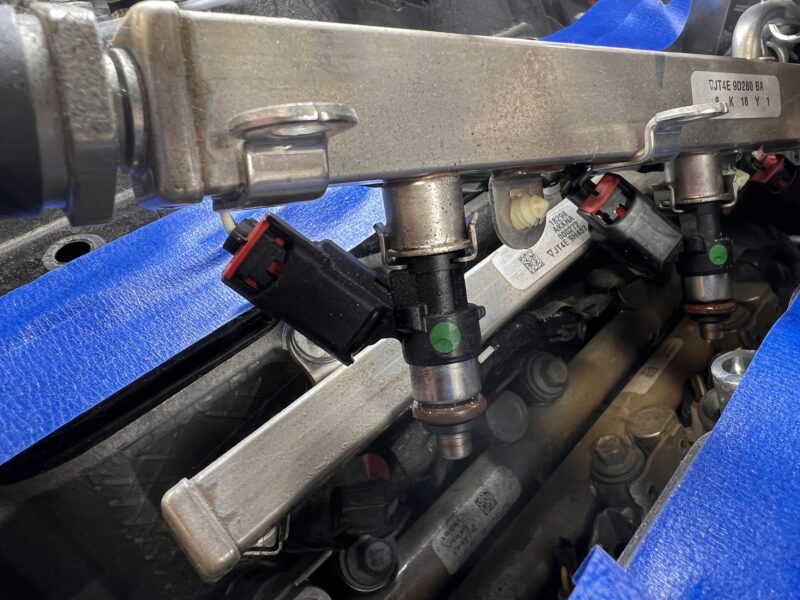
Looking down the port you can see the port injection doing its job of keeping things clean:
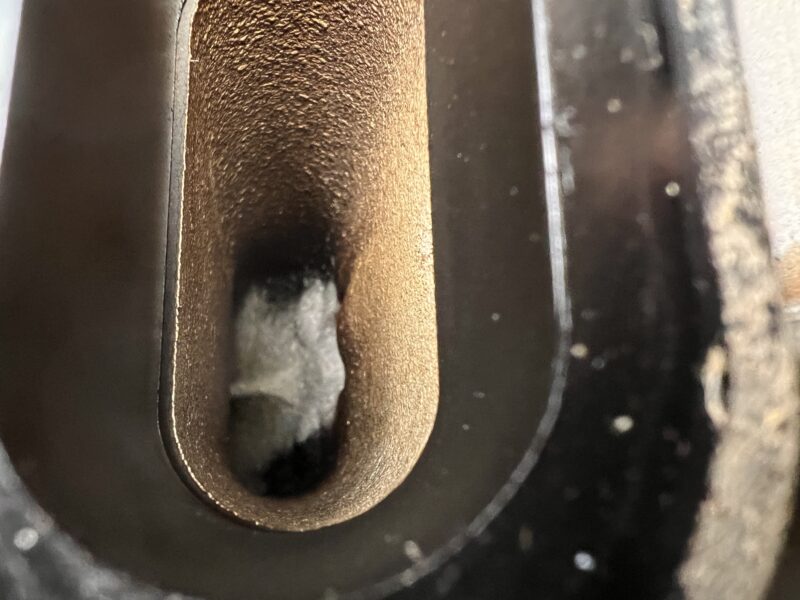
With the injectors accessible I could confirm all six were clicking when told to, so that was great news.
Next up was testing crank and cam signals. I bought the Megasquirt used, so I had to check and see what kind of sensors it was set for. I got it configured for a Hall sensor on the crank and cam, which took some fiddling and/or soldering.
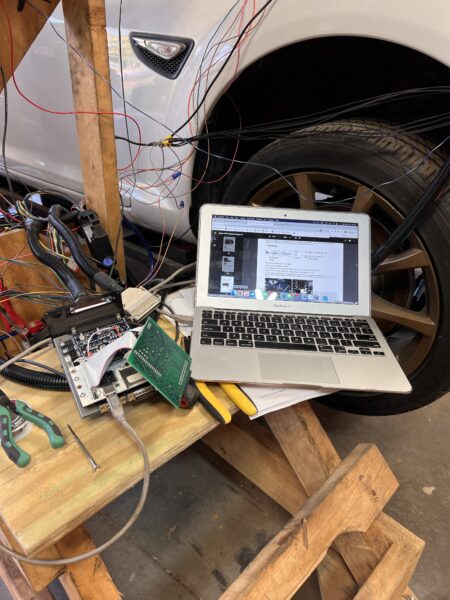
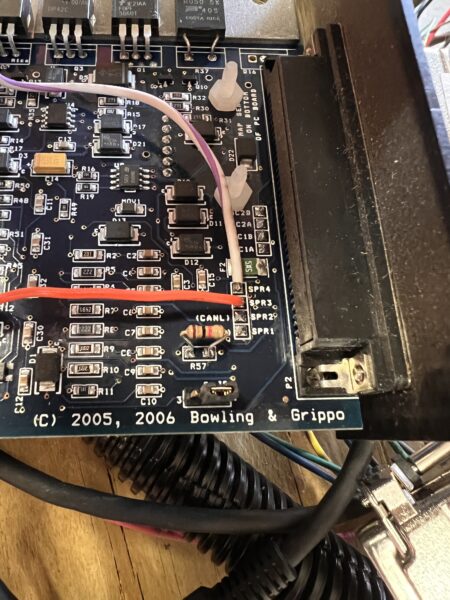
The 2.7 has no timing marks on the crank pulley, so I needed to add some. I made a little timing pointer and then pulled out my piston stop.
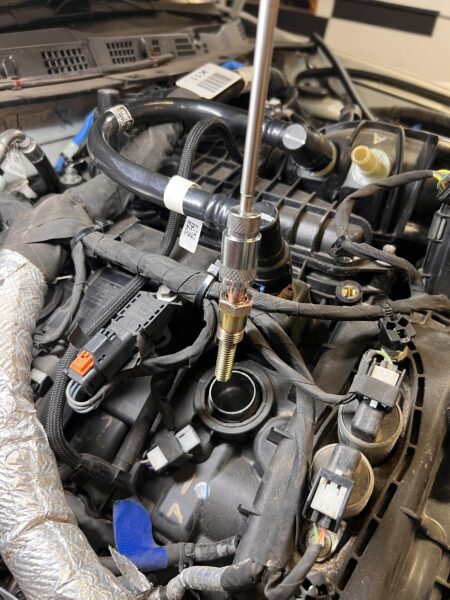
I rotated the engine in both directions and marked where the piston stopped in each direction, then set the center of those marks as TDC on the compression stroke.
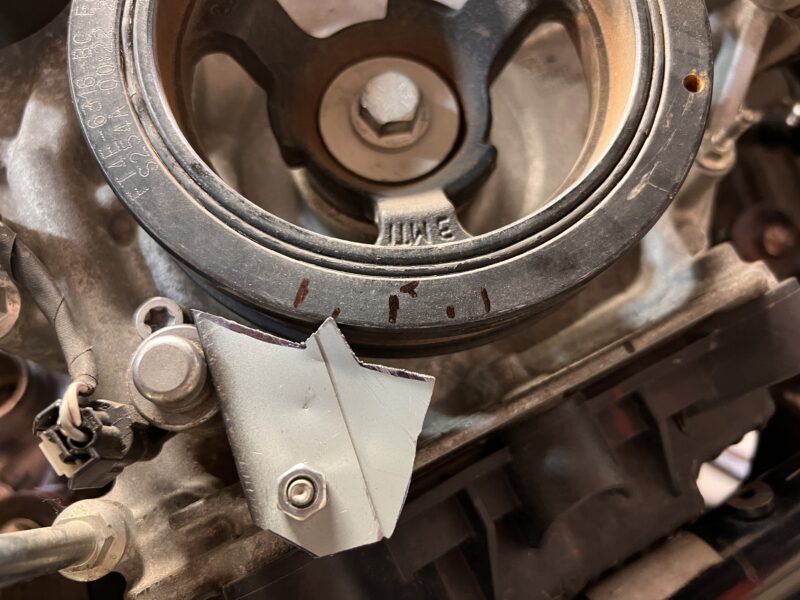
I printed off a timing wheel to get my 10/20/30 degree measurements and used a Dremel to etch those marks in place, I sure hope they're right.
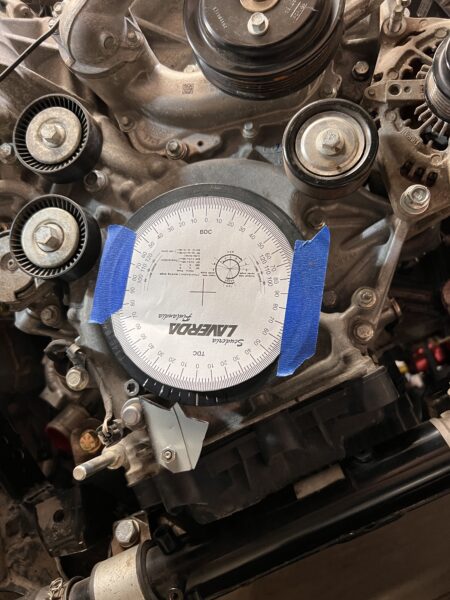
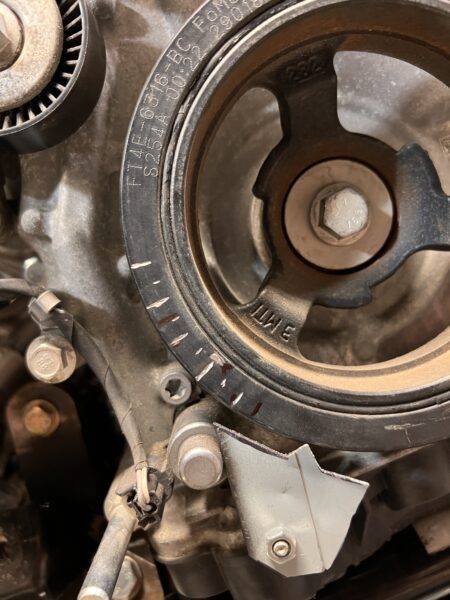
From there I was able to turn the engine over with a ratchet and see corresponding tooth inputs from the crank.

Next step will be figuring out how to see the cam inputs, then pulling the engine out, putting the flywheel in place, priming the oil system, and confirming full crank/cam sync when turning it over with the starter motor.