I have made lots of progress on my 8.8" swap, and it is ready to install and go once I get it back assembled.
1st Step was to torch off the old leaf spring pads and sway bar mounts on the 8.8", then grind them smooth.
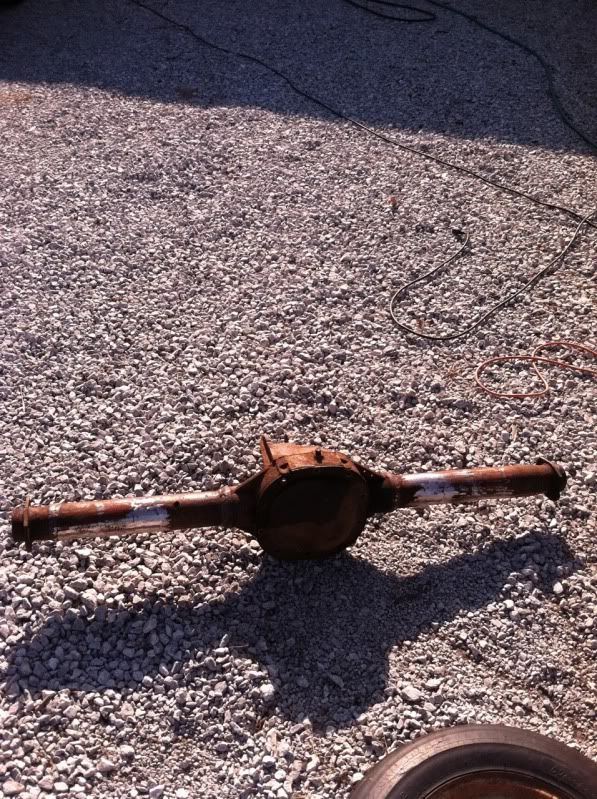
Then we carefully torched the brackets off as close as we could off the original differential. Since I didn't really give a shit about it, we torched into the housing a little ha. Oh well, axles/carrier are all good.
Then I spent about 5 hours worth of opening up the mounting points on them to fit the 8.8". Since I had that 3" section that was cut off from narrowing, I just kept fitting it to that until they all fit, and were even heights as well. 4 control arm brackets and 2 coil perches later, we were finally ready to fit the diff up into the car, install the brackets on the control arms, and start lining things up.
Now, I'm not expert, I'll say that off the bat. I'm going to explain the way we did it, which im sure is not the "professional" way of doing it.
We jacked the diff up under the car, and supported it. Using my angle finder, I got the back of the dif right at 90* to the ground. I also stuck it under the tubes to make sure they were square as well. I installed my driveshaft (with an inch of play for the trans) and bolted it to the rear end. This gave me my front to back.
To make sure one side was not farther forward, we measured center of the front hub to center of the rear dif axle hole like 10 times on either side. Always double checking. Also, we measured the downward slope of the driveshaft, trying to keep it at -2* for our pinion angle.
I'm not sure this was entirely accurate, as I didn't have the axles installed and wheels on it obviously to make sure the car was perfectly at ride height, but hell, I figure suspension is all about play, and that being a degree or so off on the pinion wouldn't kill me.
We also measured the distance between the axle flange and the outermost bracket to center the diff in the car. Once everything was set, we held the brackets toa the car still connected to the control arms and tack welded both sides. Then we continued to quadruple check all of our measurements, ensuring that we were still good.
As for the spring perches, we just eyeballed it mostly. They're pretty much parallel to the ground on top of the tube.
All in all, I think we got it pretty dam close. All our angles and distances were perfect. I suppose I'll really find out once I get it driving.
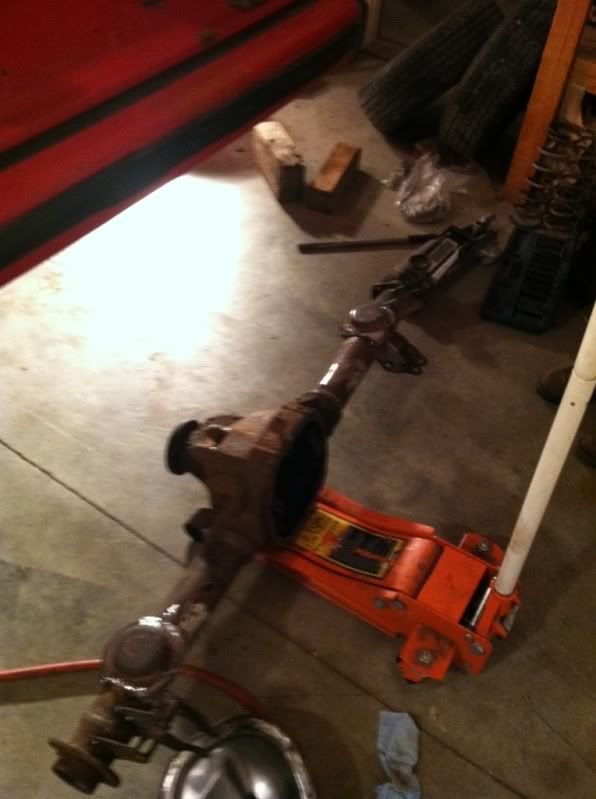
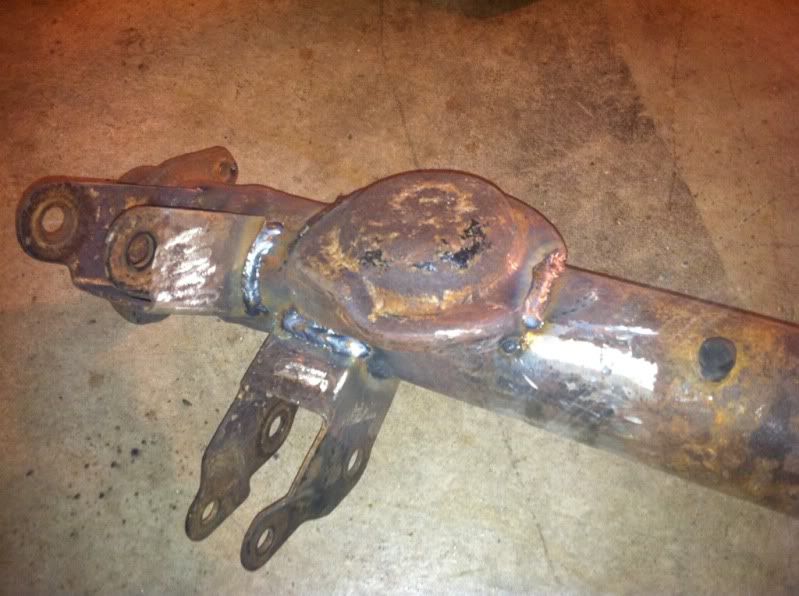
I took it with me to work, used alot of degreaser dilution and spent about 20 minutes powerwashing the crap out of the inside, and out. I immediately followed with lots of drying, and wiping as much down as I could with brake cleaner to get any remaining oils off and stall rust. Then I painted (minimal grinding, no primer, suckass job ha)
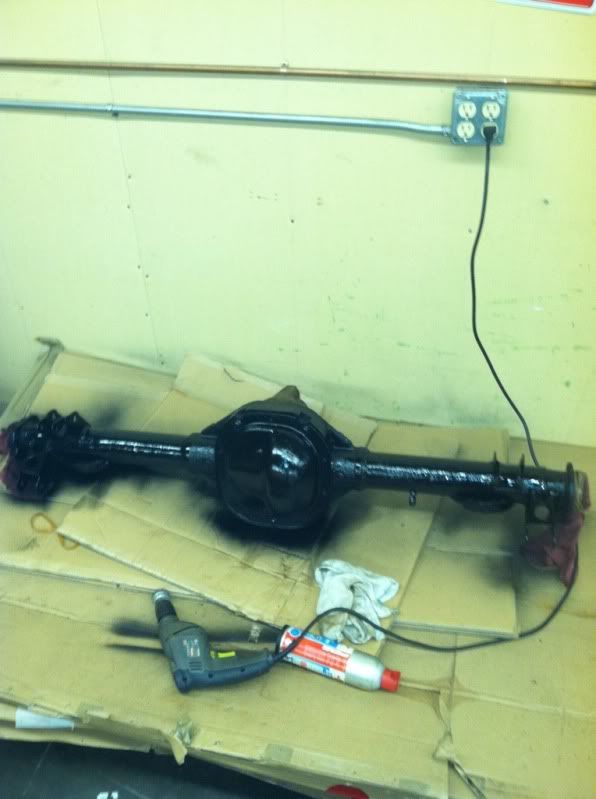
Now i'm going to drop it off at a place in town to get all the new bearings pressed in, and I'll let them re-install the pinion so I don't screw the crush sleeves up! ha.
Oh, and some comparison pictures before we really started into it:
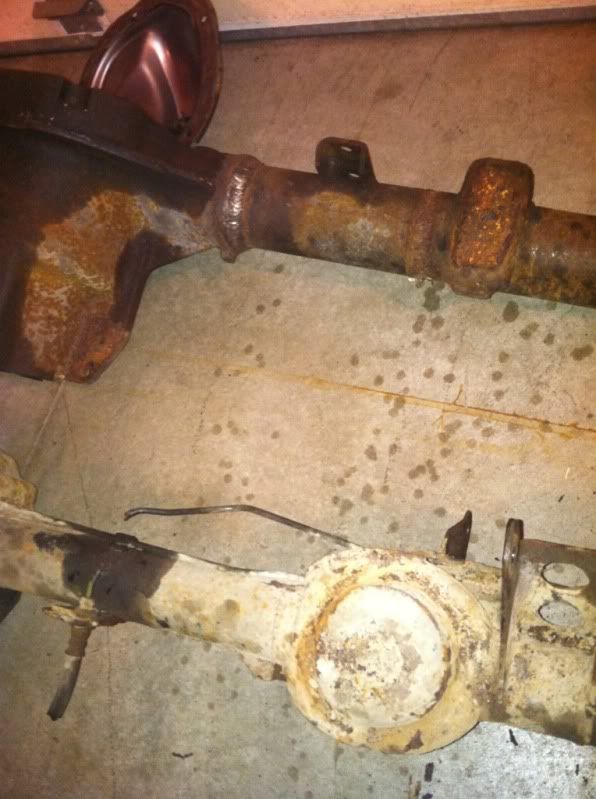
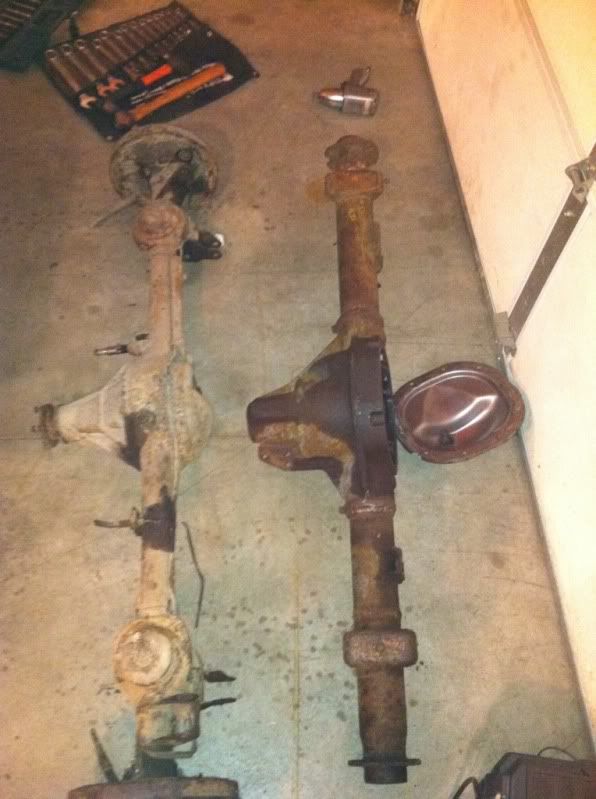
8.8 Rear End - $150 used.
*31 Spline
*3.73 Gears, Factory Limited slip.
-Narrowed 3 inches, tubes welded, Anti-lock hole welded -$210
-Other short side axle - $55
-Replacement bearings/seals/crush sleeves - ~$100
-New output shaft yoke + install - $88
-Driveshaft - $290 from Grannys.
Time spent modifying it into the car = FML